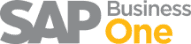
SAP Business One is a single ERP solution for managing your entire business trusted by over 80,000 small to medium sized businesses – from accounting and financials, purchasing, stock, sales, manufacturing, service, projects and customer relationships to reporting and analytics. It automates business processes, streamlines end-to-end operations and delivers a true and unified picture of business information. If you want better control over your operations, to respond to the market with greater agility and to grow, then it offers you just that.
Frontline bring the skills, expertise and experience of delivering SAP Business One. We’ve helped hundreds of customers to unlock its potential no matter their unique challenges or the market in which they operate. We’ve helped customers navigate their way to achieve the outcomes they want, and our experts can help you achieve your goals.